Helicopter > Helicopter with Flettner double rotor
Kaman K-Max 1200
K-Max 1200, scale 1 : 4,4
From mid-2023 we will be offering the K-Max 1200 model helicopter with the Flettner double rotor system. The helicopter is constructed on a scale of 1:4.4 to the original Kaman K-Max 1200 and has a rotor diameter of 3.3 m (alternatively with 2.8 m rotor diameter and modified reduction).
Attached is the report in the May 2024 issue of ROTOR magazine about the K-Max 1200.
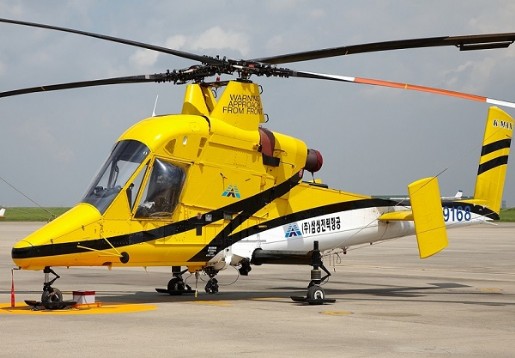
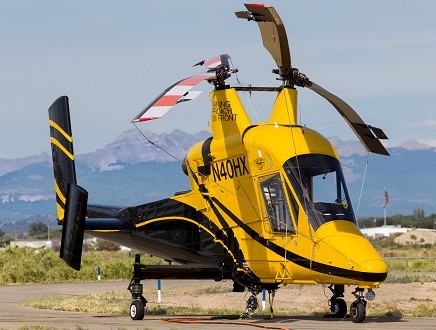
Kit K-Max 1200
- Basic prize mechanics: 3.995,- Eur
- alternatively: elektro Flettner mechanics, prepared for Hacker Q80: 3.995,- Eur
- Fuselage scale, multi-parts: price on request
- Exhaust pipe for turbine PRO-6000, stainless steel: 450,- Eur
- Landing gear, scale version (mounting kit, unpainted, without steer servo): 2.095,- Eur
- Microprocessor mixer electronics for controlling the two swashplates in the model (required to operate the model): 380,- Eur
- Kit without turbine, RC electronics, rotor blades, fuselage without painting
- Depending on the design, two different rotor diameters and head speeds are possible (rotor diameters 2.8 m or 3.3 m possible)
On request we can offer you the following components to complete the helicopter:
- Aluminum rotor blades 2.8 m Viper-X76 or 3.3 m rotor diameter M-Blade S-93
- alternatively: carbon-rotor blades 2.8 m rotor diameter
- complete RC-elektronic
- Jakadofsky turbine PJW PRO-6000
- painting of the model
- complete assembly of the kit, the RC electronics and the turbine. On request up to the ready-to-fly model
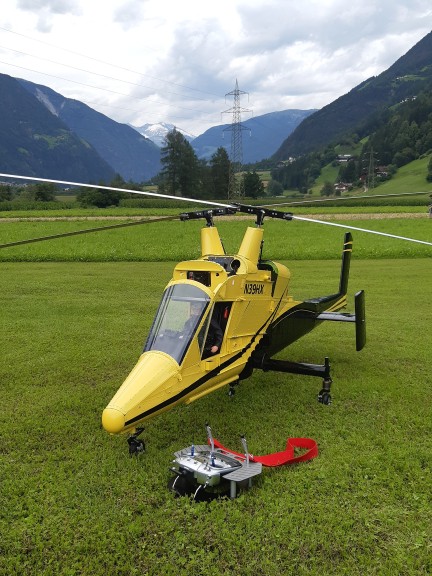
To the original, Kaman K-Max 1200
The American company Kaman recognized in 1990 that there were practically no special helicopters for the transport of external loads on the civil helicopter market. When a company needs something like this, they usually use decommissioned military machines. They are cheap to buy, but since they are usually many years old, they are very expensive to run.
Kaman therefore developed this 'Flying Truck'. Everything that is not necessary for transporting loads has been dispensed with. Two counter-rotating, intermeshing rotors are used as the rotor system. The rotor axes are arranged at an angle to one another. Torque compensation is not necessary, so the tail rotor can be dispensed with and the entire power of the drive is effectively implemented. Another special feature of the original is that the rotor blades are controlled indirectly via small flaps at the ends of the rotor blades. This eliminates the otherwise expensive and maintenance-intensive hydraulic system for controlling the rotors.
The cell of the original is made in conventional aluminum construction. The fuselage is kept as narrow as possible to give the pilot an optimal view to both sides and, above all, downwards. The cell only offers a place for the pilot. For special work such as checking high-voltage lines, two seats can be hung on the side of the fuselage. The passengers then sit in the open air and thus have an optimal all-round view.
The first prototype of the K-Max 1200 made its maiden flight on December 23, 1991. The first production helicopter followed about two years later (on January 12, 1994).
The principle of the K-Max 1200 is based on the design principle of the FI-282 "Kolibri". The German Anton Flettner designed this new type of helicopter during the war years from 1938 and solved the problem of torque balancing with counter-rotating, intermeshing rotors - the Flettner double rotor was born.
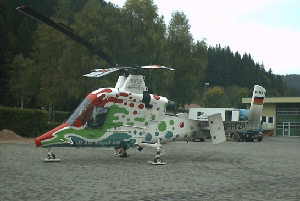
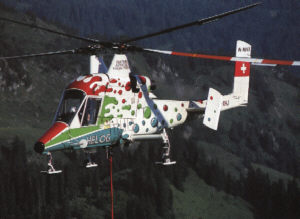
K-Max 1200 from the Swiss company Helog transporting loads
Kaman K-Max 1200 in use by Heli Air Zagel AG, shortly before being used for forest liming at Schluchsee/Black Forest. Here in a particularly complex but interesting paint job
Technical specifications Kaman K-Max 1200, original
- crew: 1
- engine: gas turbine Lycoming T53-17A
- power: 1343 kW
- overall length: 15.85m
- rotor diameter: je 14.73m
- empty weight: 2300kg
- max. hook load: 2720 kg
- MTOW: 5215 kg
- max. speed: 185 km/h
Technical specifications Kaman K-Max 1200, scale model 1 : 4,4
- rotor diameter: 3.3 m (depending on the reduction gear, a rotor diameter of 2.8 m or 3.3 m can be selected)
- rotor angle: between the the two rotor axes 24°
- overall length: 353 cm
- body length: 282 cm
- body width: 29 cm
- width over all: 88 cm (width of the landing gear)
- Width over the tailplanes: 65 cm
- body height: 73 cm
- height above all: 95 cm
- engine: Jakadofsky PJW-Turbine PRO 6000 (alternativ: JetCat SPT10-H oder elektrisch mittels Hacker Q80)
- mechanics: robust industrial standard, completely in precision CNC aluminum production and carbon
- rotor head: 2 pcs. 2-blade rotor heads, completely in aluminium, blade bearing shaft 12 mm diameter, blade grip 22 mm
- power transmission: 3-stage reduction gear, last gear stage running in an oil bath
- rotor head speed: ca. 770 rpm (depending on the rotor diameter)
- swashplate control: 6 x servos KST X20-3612 for the 3-point linkage of the two swashplates, other servos on request)
- FBL system: all commercially available 3-axis stabilization systems can be integrated (e.g. Bavarian Demon 3X, Beast-X)
- fuel: kerosene/oil mixture (5% oil content)
- tank system: 3.5 ltr. tank (kevlar), incl. hopper tank (iTrap 60), Festo-connectors
- take-off weight: approx. 32 kg
- mixer: electronic swashplate mixer
- mixing functions: control of the two swashplates (120° mixer) for the pitch, pitch, roll and yaw functions
- control of nose wheel, elevator and rudder
- lighting, scale execution
Description of the Flettner mechanics for the K-Max 1200
As already described, the complex mechanics of the model helicopter were developed entirely using 3D software. This is the only way to achieve the greatest possible planning security right from the start. All components are then manufactured based on the derived drawings and fit and function as planned right from the start.
The narrow silhouette of the fuselage proved to be very problematic when converting the original into the model construction. For example, to implement the extremely narrow dome construction of the original, a special gear configuration was chosen.
About the drive: the PJW turbine "PRO 6000" located behind the mechanics transfers the power to the two main rotors via a 3-stage gearbox. The two rotors are coupled to each other via the middle pair of gears and are decoupled from the drive via a freewheel during autorotation.
In addition to the PJW turbines from Jakadofsky, it is also planned to use the SPT10 from JetCat or, as an electric version, the Q80 from Hacker.
The PJW turbine sits at the same height as the original K-Max 1200. A prototypical exhaust system is offered to extend the exhaust pipe. When using the JetCat SPT-10, the turbine is below the mechanics. The turbine outlet is prototypically located in the correct position in the K-Max 1200 model via a special exhaust pipe.
As usual, the entire mechanism is precision CNC-manufactured (aluminium 7076-T6, all parts are black anodized). The RC-stem, the canopy, the complete rear and many other parts are made of carbon.
Technical description:
- counter-rotating, intermeshing 2-blade double rotor system based on the Flettner principle
- very compact mechanics
- all CNC parts are made of aerospace aluminum (EN AW-7075 T6, black anodized) and carbon
- 3-stage reduction gear (or 2-stage with electromechanics), last stage running in an oil bath (completely encapsulated)
- linkage of the two swashplates via 3 servos each, free of play 120° linkage
- all ball heads on the two swash plates and rotor heads are made of steel
- more than 40 bearings installed
- rotor shaft diameter 15 mm
- swashplate driver with full ball bearings
- blade bearing shaft diameter 12 mm
- rotor blade connection dimension 22 mm, 6 mm bore
- industrial quality finish
- detailed assembly and adjustment instructions
- assembly kit, assemblies that are difficult to assemble are supplied pre-assembled

View of the mechanics with the Jakadofsky PRO-6000 turbine and the special exhaust system for the K-Max 1200
Some CAD images of the K-Max 1200 assembled with the adjacent mechanics. Also shown are the future versions of the mechanics with the JetCat SPT10-H turbine and the Hacker Q-80.
And some CAD images showing the level of detail of the nose and rear landing gear of the K-Max 1200
Electronic mixer for the Kaman K-Max 1200
A special mixer electronics is required to control the two swash plates, which we also offer as an accessory. This electronics is connected in the model between the receiver and the swash plate servos. The advantages of such electronics are that important parameters can be changed quickly by changing the software. An associated programming module can be connected to the electronics in the model via a network cable. This can then be used to adjust all parameters in the workshop or on the airfield.
The model helicopter can be controlled like any other helicopter. Any normal remote control transmitter can be used as a transmitter without special mixers on the transmitter side.
A 3-axis flybarless system can also be easily integrated, see below.
The following functions are supported by the mixer electronics:
Processing of the signals for collectiv, roll, pitch and yaw from the receiver to control the two swashplates with 3 high-performance servos per swashplate, i.e. a total of 6 servos to control the two swashplates.
A stabilization system (e.g. Heli Command, V-Stabi, Beast-X etc.) or individual gyro systems (e.g. GY-401) for individual axes can also be looped in between the receiver outputs and the mixer electronics.
Alternatively, a Pixhawk 4 can also be used in the future. The special programming required to control the two swashplates is in preparation
Reprint only with permission of the author. All statements without guarantee.